Eaton’s Auburn, Indiana, Clutch Facility Improves Material Flow and Safety
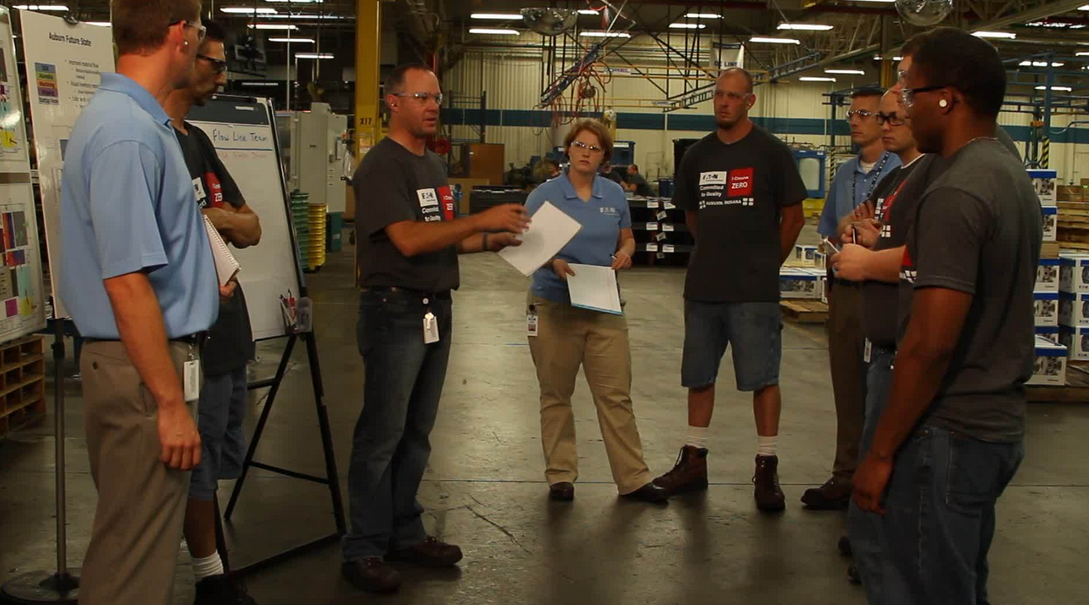
A cross-functional team of employees at Eaton’s Auburn, Indiana, facility worked together to improve material flow and improve safety, ergonomics and efficiency.
Power management company Eaton has announced that its plant in Auburn, Indiana, has reduced the distance material and parts travel through the plant by 4.5 miles per day to help improve safety, ergonomics and efficiency.
The improvements are part of the plant’s Material Flow Project.
The Auburn facility designs, engineers and manufactures clutch components for the global commercial vehicle industry. The Material Flow Project was initiated last year to address changes to Auburn’s product mix and growing production volume – more than 50 truckloads of material a day come in and out of the facility.
“The project was a real team effort that involved machining, assembly, production, maintenance, materials, engineering and safety,” said Ralph Beam, Auburn’s plant manager.
Team members conducted a thorough analysis of Auburn’s overall manufacturing footprint and individual production cells, material storage, work in process, sub-assemblies, finished goods, packaging and shipping areas. They identified a 23-step improvement plan that ranged from moving equipment closer to workers and making greater use of transport carts to installing full-size bearing presses and relocating robotic cells and entire assembly lines. The project was completed in October.
As each step was implemented, production operators, supervisors and engineers responsible for the affected cell worked together to identify other opportunities for improvement. In one area, a new hoist with multi-speed controls was installed that is much easier for workers to operate than the previous system. Visual alerts have been added to trigger inventory replenishment within cells, and material now is delivered to the edge of the various work cells to eliminate forklift traffic within cells.
Safety improvements included installing additional guards, bumpers and emergency stop switches. New visual controls identify safety equipment and procedures.
In conjunction with the Material Flow Project, Auburn employees installed high-efficiency lighting and fixtures from Cooper Industries, which Eaton acquired last year. Combined, the new fixtures and sensors save more than 600,000 kilowatt hours of electricity per year and provide a brighter work environment. Also added was a high-efficiency air compressor that reduces electricity and gas consumption by 4.4 percent and 17.2 percent, respectively.
The Auburn plant employs more than 175 people. Eaton contributes nearly $200 million annually to Indiana’s economy through taxes, wages and supplier impact. In addition, the Auburn facility and its employees donated $10,750 to local community organizations in 2012.
About Eaton
Eaton is a power management company providing energy-efficient solutions that help our customers effectively manage electrical, hydraulic and mechanical power. A global technology leader, Eaton acquired Cooper Industries plc in November 2012. The 2012 revenue of the combined companies was $21.8 billion on a pro forma basis. Eaton has approximately 102,000 employees and sells products to customers in more than 175 countries. More information at: www.eaton.com.
Category: General Update